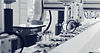
Solutions
Machinery
Series 300
Type 302
The Type 302 is a rotary washing system designed for cleaning ampoules, bottles, cartridges, vials, and various other containers.
Key Features
- Outputs up to 24,000 containers per hour
- Smooth container handling with coated grippers
- Infeed options from trays or an upstream machine
- Available ultrasonic bath and recycling station
- Optional water heating up to 85°C / 185°F
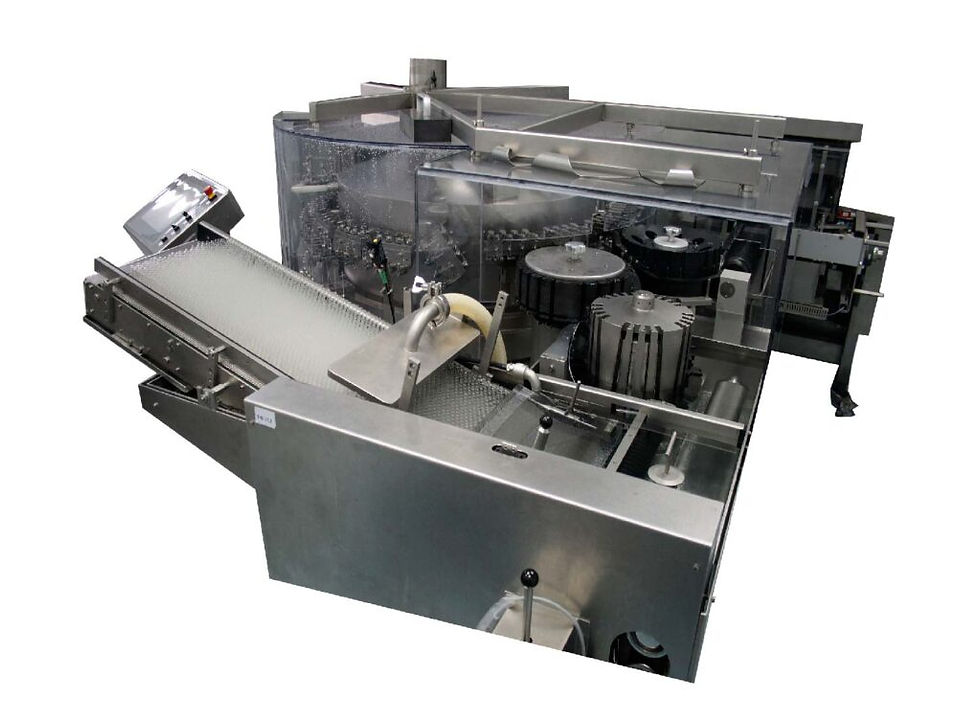
Type 303/304/305
The Type 303/304/305 machines are designed to wash vials, syringes, cartridges, and ampoules. They clean and dry both the inside and outside of the containers, achieving up to a 3-log reduction in contaminants.
Key Features
- Outputs up to 9,000 containers per hour
- Constructed from high-grade stainless steel and
pharmaceutical-grade plastics
- Smooth container handling with coated grippers
- Optional cost-effective WFI recycling unit
- Compatibility with various cleaning agents
- Energy-efficient cleaning needle design
- Needle movement ensures thorough cleaning of the
entire container interior
- No glass-to-glass contact during cleaning cycles
- Optional siliconization with servo-controlled needle
movement for customized silicone patterns

Type 306
The Type 306 is a semi-automatic washing machine designed for smaller scale operations, suitable for ampoules, vials, syringes, bottles, and cartridges.
Key Features
- Outputs up to 1,500 containers per hour
- Manual loading
- Cleans the inside and outside of the containers
- Quick size changes
- Intermittent spray of media synchronizes with the
transport system
- Up to 12 stations with 3 different cleaning media
- Optional recycling station

Type 308
The Type 308 is a high-speed machine designed to wash ampoules, cartridges, syringes, and vials. Featuring an innovative balcony design, it allows operators to maintain visual contact with the process. Fully customizable, it offers modules for inside and outside cleaning, inner and outer blow drying, siliconizing, tip cap or needle shield application, and the use of various cleaning agents.
Key Features
- Outputs up to 36,000 containers per hour
- Containers are fed automatically from an upstream
machine or manually from trays
- Ultrasonic bath for pre-cleaning of the objects
- No glass-to-glass contact using coated container
grippers
- Specialized cleaning needles designed to improve
energy efficiency
- Servo motors positioned along the line guarantee the
alignment of the containers with the washing and
drying needles
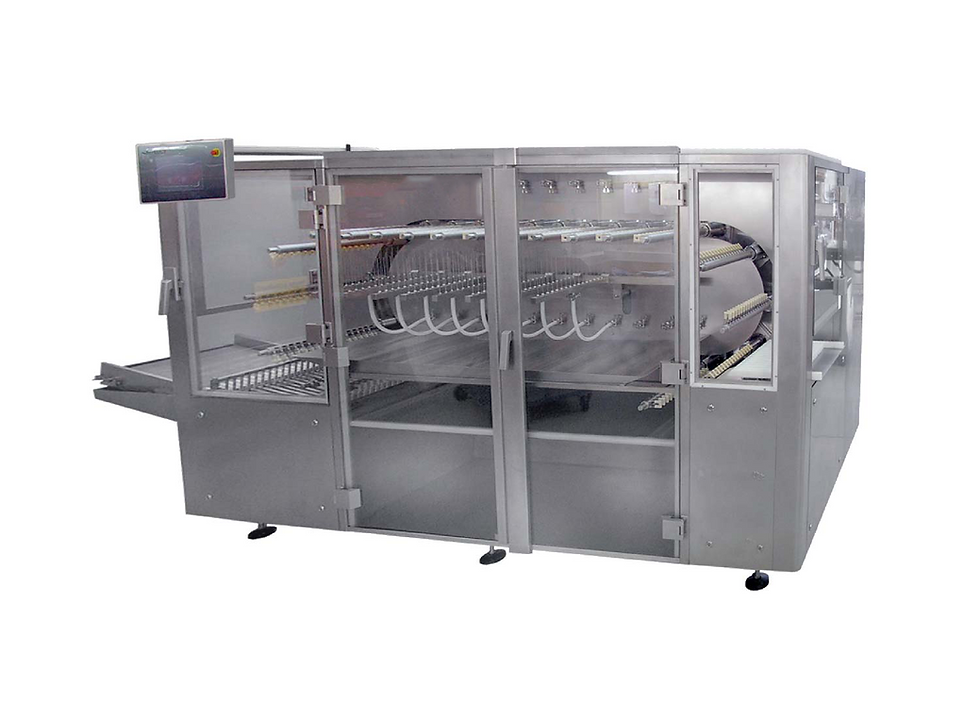
Type 309
The Type 309 machine is a fully automatic, continuous washing system designed for the external cleaning of ampoules, vials, and bottles. It washes, rinses, and dries the external surfaces of the containers, which are then discharged into trays or sent to downstream processing.
Key Features
- Outputs up to 21,000 containers per hour
- Flexible and compact design allows for customized
cleaning cycles
- Easy access to the cleaning stations and for size
changes
- Quick and easy size changeovers to process container
sizes up to 95 mm in diameter and 180 mm in height
- Specialized cleaning needles designed for ideal results
and improved energy efficiency
- Sterile hot air blow drying parameters are adjustable
via the operator interface terminal
- Optional recycling station, Type 705, provides cost
efficient reconditioning of used cleaning agents

Series 400
Type 401-40X
The Type 400 series machines offer hot air sterilization for glass ampoules, vials, syringes, and cartridges. The depyrogenation process is divided into three main zones: 1) Pre-Heating, 2) Depyrogenation, and 3) Cooling. These machines can be seamlessly integrated into downstream processing.
Key Features
- Outputs up to 610 kg per hour
- Air convection pre-heating and sterilizing zone for
energy efficiency and gentle heating of the containers
- Containers are fed automatically from an upstream
machine or manually using trays
- Temperature and differential pressure indicators
ensure ideal and repeatable machine settings
- Temperature distribution is achieved by multiple
control sensors
- PLC for system control and monitoring of relevant data
- Servo-controlled baffles aid in cross-flow regulation

Type 411
The Type 411, Puv-A-Tech™, is an enclosed sterile transfer chamber utilizing pulsed ultraviolet radiation light to decontaminate outer surfaces. This technology achieves up to a 6-log reduction within 5-30 seconds of exposure time.
Key Features
- Machine designed as a pass-through into a cleanroom
or isolator
- Components are placed into the chamber by an
operator or robotic arm, and the door is closed to
contain the process
- Complete cycle (loading, exposure, and unloading)
decontaminates the entire interior of the unit and
container surfaces within 20-60 seconds
- Components are removed and ready for the next
processing stage
- 100% verification on every cycle
- Available as a stand-alone or in-line machine

Series 500
Type 502/503
The Type 502/503 machines combine the filling and closing of ampoules into one single compact unit.
Key Features
- Outputs up to 6,000 containers per hour
- A transport star wheel provides smooth and
continuous transfer of the objects to the working
stations
- Two-piece, valveless dosing pumps provide precise
dosing with filling accuracy up to +/- 0.05%
- The containers are continually rotated to minimize
foaming of the product and ensure an evenly heated
ampoule stem, leaving a perfect dome
- Vials are closed with rubber stoppers, fed from a
vibrating bowl
- Optimized for use under laminar flow, RABS, or isolator
- The machines can be used as stand-alone units or
integrated into a production line

Type 504-506
The Type 504/505/506 machines are designed for filling and closing both open and pre-sealed ampoules. Their design enables quick and easy changeover from ampoules to vials.
Key Features
- Outputs up to 24,000 containers per hour
- Rotary-style machine provides smooth and gentle
continuous transport of the objects
- System control via PLC
- User-friendly touch screen operation
- Rotation of the object minimizes foaming of the
product and ensures an evenly heated ampoule stem,
leaving a perfect dome
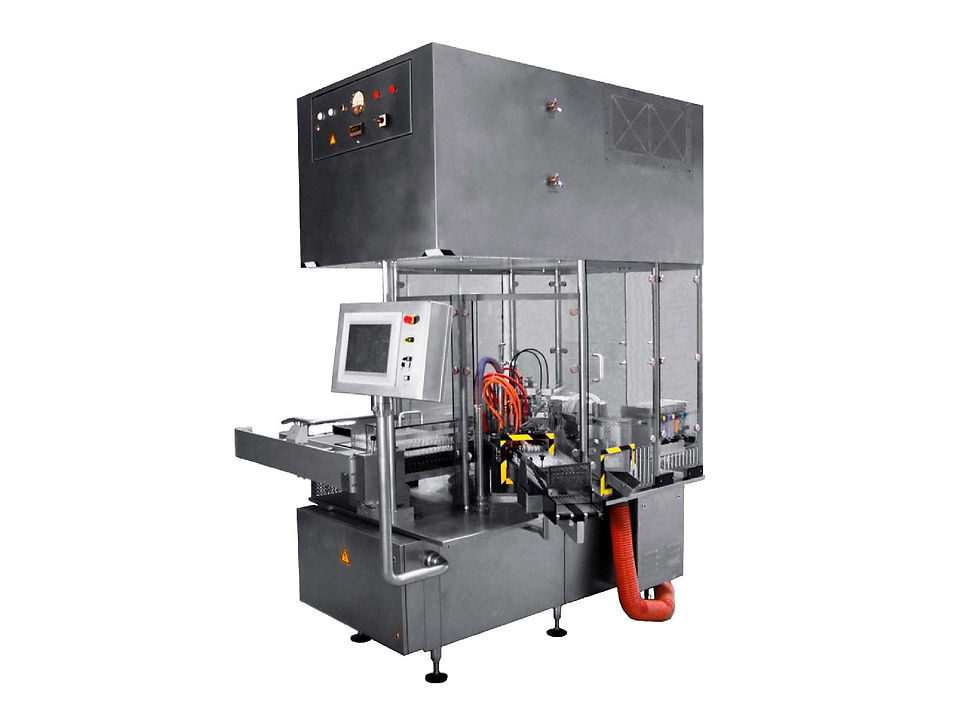
Type 515
The Type 515 is a filling and closing machine designed for vials and syringes. Optimized for use under laminar flow and constructed from high-grade stainless steel, this machine ensures optimum hygienic performance.
Key Features
- Outputs up to 3,600 containers per hour
- Liquid filling
- Highly flexible and compact design
- Containers are transported into a star wheel that
moves them to different processing stations
- Filling needles are controlled by a servo drive for fast
and accurate dosing
- Ultra-high filling accuracy
- Stoppering is fed through a sorting bowl, picked up by
a vacuum tool, and precisely inserted
- Few size parts, quick changeover from vials to syringes
- Integrated inspection system
- Laminar flow and/or isolator friendly design
- Can be used as a stand-alone machine or integrated
into a complete processing line

Type 515 Plunger Rod Assembly
The Type 515 combines high-speed plunger rod insertion and labeling of syringes in a single unit. At the heart of the machine is an automated transport star wheel that moves products through four different stations, enabling the assembly of up to 40 syringes per minute. At the first station, a pneumatically actuated gripper assembly picks up a plunger rod from the end of the vibratory track and uses a 2-axis robotic arm to thread it into a syringe. At the second station, backstops are carefully placed on the flange of each syringe. The third and fourth stations check for the presence of the plunger rod and backstop.
Key Features
- Outputs up to 2,400 syringes per hour
- Compact machine design with integrated control
cabinet
- High precision plunger rod insertion
- Monitored torque for ideal closing results
- Camera inspection checks for proper plunger rod and
backstop placement
- Optional labeling station available

Type 529
The Type 529 semi-automatic filling and closing machine for flexible bags sets new standards in the pharmaceutical market. It is capable of processing all bag types (EVA, PVC, PP) with fill volumes ranging from 50 mL to 5 L.
Key Features
- Available in tabletop, dual, semi-automated conveyor,
and fully automatic versions
- Ideal for lab trials (1 filling head) and production (2-4
filling heads)
- Peristaltic or mass flow filling method options
- Attached flow regulator for high filling accuracy
- Automatically cuts pre-sealed tubes for filling
- Stoppering and heat/RF/ultrasonic sealing
- Manual or conveyor belt transport system
- Integrated closing system eliminates product
contamination
- Compatible with Laminar Flow and light curtain
systems

Type 534
The Type 534 is an automated filling and closing machine designed for vials, bottles, and other free-standing containers. Its modular design allows for easy customization to meet specific customer requirements.
Key Features
- Outputs up to 9,000 containers per hour
- Good accessibility to all workstations with inline design
- Adjustable walking beam transport for different
container sizes
- Servo-controlled filling needles for precise filling
tolerance up to +/- 0.05%
- Up to 100% in-process control verification
- Sorting bowls for closures such as stoppers and caps
- Vacuum-activated placement of stoppers into vials
- Torque-monitored crimp capping
- Separate container reject and discharge lanes
- Compatible with RABS, Laminar Flow, and/or isolator
systems

Type 535
The Type 535 machine is designed to fill and close nested vials, syringes, and other nested containers. It is the ideal solution for manufacturers seeking to automate and/or validate the filling of products in clinical trials or during the development phase.
Key Features
- Outputs up to 4,600 containers per hour
- Manual nest loading and unloading
- Turn table in-feed and out-feed
- Rotary piston pump, peristaltic pump, or time pressure
filling options
- 6-Axis clean room robot or X-Y transport system
- Sorting bowls for closures
- Filling and closing under vacuum to reduce
contamination and bubble formation
- Compact machine design with integrated Laminar Flow
- Machine guarding for optimum user safety
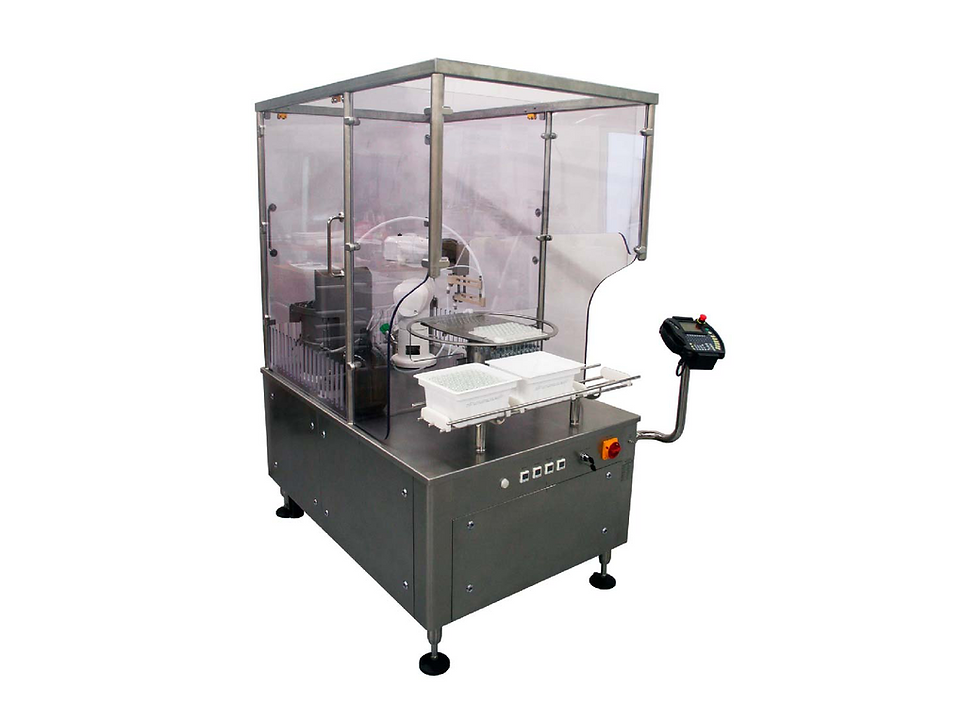
Type 543
The Type 543 filling and closing machine is designed to process vials, syringes, and cartridges with either intermittent or continuous motion throughout the machine. Its modular design allows for easy adaptation to customer-specific requirements.
Key Features
- Outputs up to 10,000 containers per hour
- Rotary piston pump, peristaltic pump, or time-pressure
dosing options
- Customized stoppering station with vacuum assist
- Direct in-line verification with camera system
- All parts in contact with the product can be easily
disassembled and sterilized
- Quick and easy size changeovers
- Containers are transported separately in individual
holders, which can be quickly changed for different
size containers
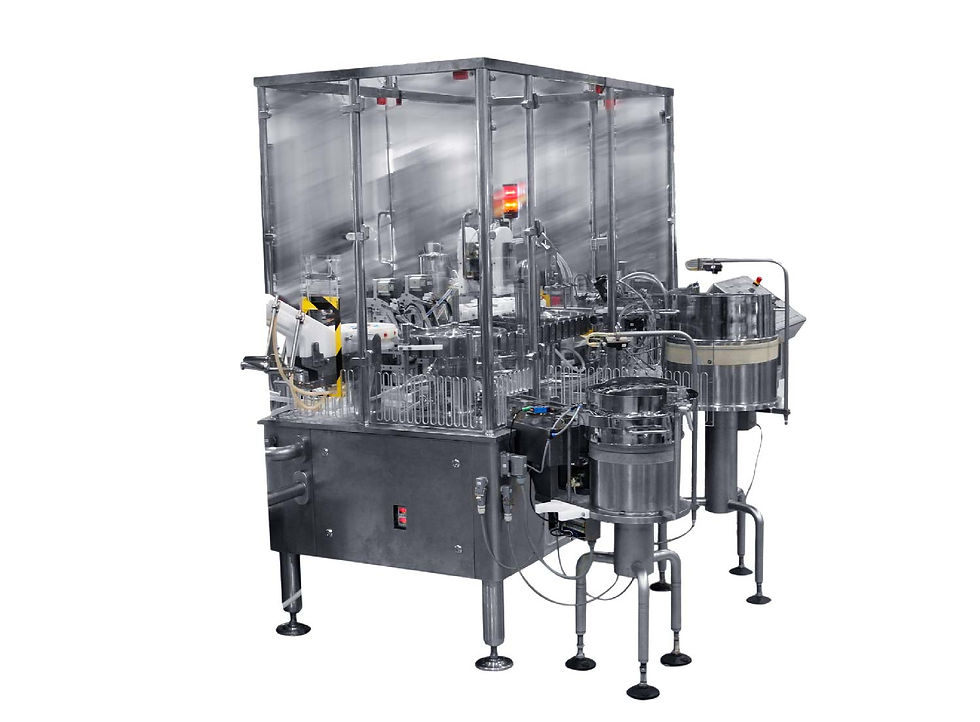
Type 550
The Type 550 machine features a high-speed, continuous motion balcony design for the filling and closing of vials and cartridges. Its servo drive technology ensures maximum versatility and repeatability.
Key Features
- Outputs up to 36,000 containers per hour
- Processes standard and freeze-dried rubber stoppers
- Best suited for through-the-wall installations
- Adjustable main transport system for quick and easy
size changeovers
- Containers are separated and individually fed to the
main transport system
- Optional pre- and post-gassing available
- Integrated inspection system to reject faulty
containers
- Precision force control for crimping and integrated
visual inspection system ensures proper sealing
- Balcony design provides optimized laminar flow
friendly operation inside a Class A clean room and can
be directly combined with an isolator or a rapid access
barrier system (RABS)

Type 570
The Type 570, Vers-A-Tech™ is a semi- or fully-automatic machine designed to accelerate the packaging of Cell & Gene Therapy products, handling both bags and nested containers on a single platform.
Key Features
- Flexible pick & place modular platform
- Automatic robot technology for all processing
- Compatible with isolator and/or laminar flow systems
- Compatible with lyophilization transfer chambers
- Robot fills and stoppers nested containers
- Filling by peristaltic pump with disposable fill kits
- Custom nest holder for easy transfer of nested
containers in and out of the processing system
- Robot picks up a bag, inserts the open tube into the
filling needle, and then seals the tube

Series 600
Type 601/602
The Type 601-602 machines are compact, fully automatic systems designed for printing and applying self-adhesive labels to vials, bottles, syringes, ampoules, and cartridges. These continuous motion labelers can be integrated into a production line or operated as stand-alone machines.
Key Features
- Outputs up to 24,000 containers per hour
- Containers are automatically fed from an upstream
machine or manually using trays
- Individual transport of containers to the labeling
station by a star wheel
- Transport wheel designed with pockets for safe and
gentle handling of containers
- Precision servo control label dispenser for self
adhesive labels
- Label dispenser is adjustable for different sizes
- Label dispenser is controlled by a stepping motor and
can be equipped with additional devices such as a bar
code scanner, printer, or checking units
- User-friendly touch screen operation
- Easily exchangeable size parts allow for various
container sizes
- Containers are discharged into trays
- Station can be equipped with a hot-foil, thermal
transfer, laser, or ink jet printer
- Horizontal and vertical adjustments of the printer adapt
to different print areas
- Rubber roller dispensing station ensures smooth label
application on containers

Type 603
The Type 603 is a fully automatic labeling machine designed for applying self-adhesive labels to vials, cartridges, ampoules, and other special containers. It can function as a stand-alone labeler or be integrated into a fully automatic production line.
Key Features
- Outputs up to 36,000 containers per hour
- Quick, tool-free size part changes
- Easy accessibility to all working stations
- Smooth, continuous container transport
- Automatic rejection of nonconforming objects
- Safety system ensures user protection
- User-friendly touch screen operation
- Integrated electronic control cabinet in the machine
base
- Can be equipped with a bar code scanner, vision
system, and various printer types

Type 604
The Type 604 is a fully automatic, linear machine designed to apply self-adhesive labels to bottles. Labels are printed by a hot foil, thermal transfer, or laser printer and then transferred to the labeling station. Containers are fed from an upstream machine by a rotary table or conveyor to complete the label application process.
Key Features
- Outputs up to 12,000 containers per hour
- Highly flexible and compact design
- Label dispenser unit with servo technology
- Automatic speed synchronization
- User-friendly touch screen operation and system
control via PLC
- Accurate placement of labels on containers
- Options available for barcode scanner, label position
and presence check, and printer

Type 607
The Type 607 is a compact machine that combines high-speed plunger rod insertion, backstop assembly, and labeling of syringes. It can process various types and sizes of syringes, plunger rods, and backstops with the use of interchangeable size parts.
Key Features
- Outputs up to 24,000 syringes per hour
- Servo-controlled main drive and rotation motion of the
syringe produce precise and constantly monitored
torque
- Rotary movement of syringes to ensure smooth
positioning
- Torque feedback allowing for automatic adjustment of
insertion
- Integration of hot foil, inkjet, or laser printers
- Vision system for validating correct label information
- Automatic rejection of non-conforming containers
- Can be used as a stand-alone machine or integrated
into a processing line

Series 700
Type 703
The Type 703 tray loader is a precise and compact solution for loading containers into trays. It can handle various sizes of vials, bottles, syringes, ampoules, cartridges, and other stable standing containers. A fully integrated camera system ensures all quality standards are met.
Key Features
- Outputs up to 36,000 objects per hour
- Adjustable infeed guides to process various container
sizes
- Transport of containers to the loading station via servo
driven transport belt
- Configurable for various types of trays (e.g., stainless
steel, cardboard, 3-sided trays)
- Camera verification system
- Automatic rejection of non-conforming objects

Type 728
The Type 728 is a visual inspection machine for bags utilizing the Tyndall effect. Bags are fed from an upstream conveyor into the inspection station, where they are analyzed multiple times by rotation. Non-conforming bags are rejected and not mixed with good bags. Upgradable features include conveyor belt infeed, report data printing, dark protection curtains, and spare/wear parts.
Key Features
- Non-conforming bags are rejected from the machine
- Upgradable features include conveyor belt infeed,
report data printing, dark protection curtains, and
spare/wear parts
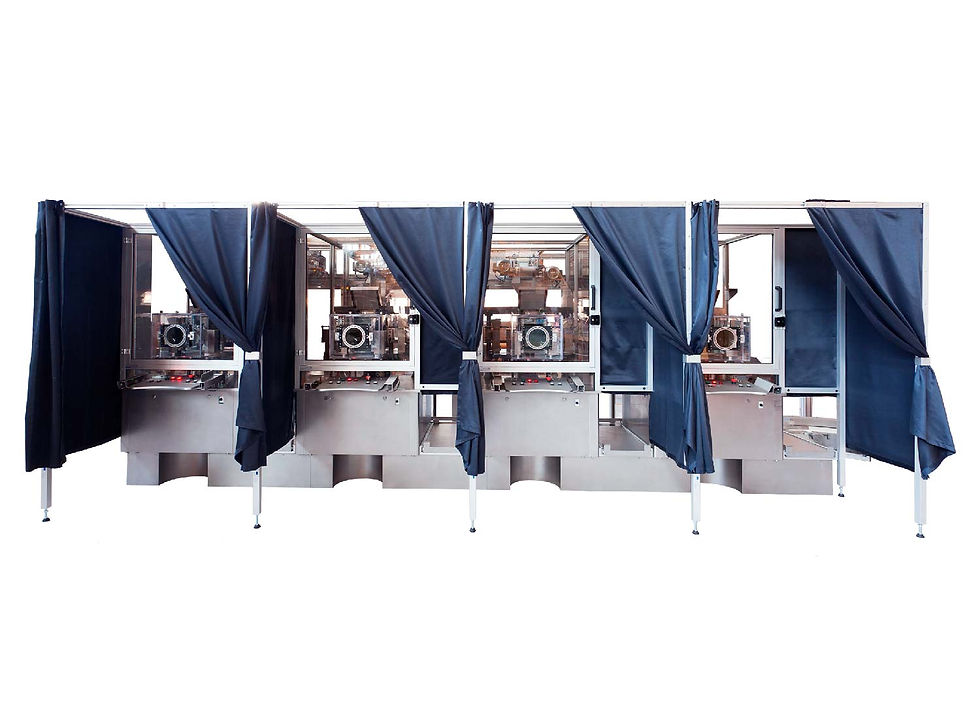
Machines by Series
Series 300

Type 303/304/305
Key Features
- Outputs up to 9,000 containers per
hour
- Constructed from high-grade
stainless steel and pharmaceutical
grade plastics
- Smooth container handling with
coated grippers
- Optional cost-effective WFI
recycling unit
- Compatibility with various cleaning
agents
- Energy-efficient cleaning needle
design
- Needle movement ensures thorough
cleaning of the entire container
interior
- No glass-to-glass contact during
cleaning cycles
- Optional siliconization with servo
controlled needle movement for
customized silicone patterns
The Type 303/304/305 machines are designed to wash vials, syringes, cartridges, and ampoules. They clean and dry both the inside and outside of the containers, achieving up to a 3-log reduction in contaminants.

Type 306
Key Features
- Outputs up to 1,500 containers per
hour
- Manual loading
- Cleans the inside and outside of the
containers
- Quick size changes
- Intermittent spray of media
synchronizes with the transport
system
- Up to 12 stations with 3 different
cleaning media
- Optional recycling station
The Type 306 is a semi-automatic washing machine designed for smaller scale operations, suitable for ampoules, vials, syringes, bottles, and cartridges.
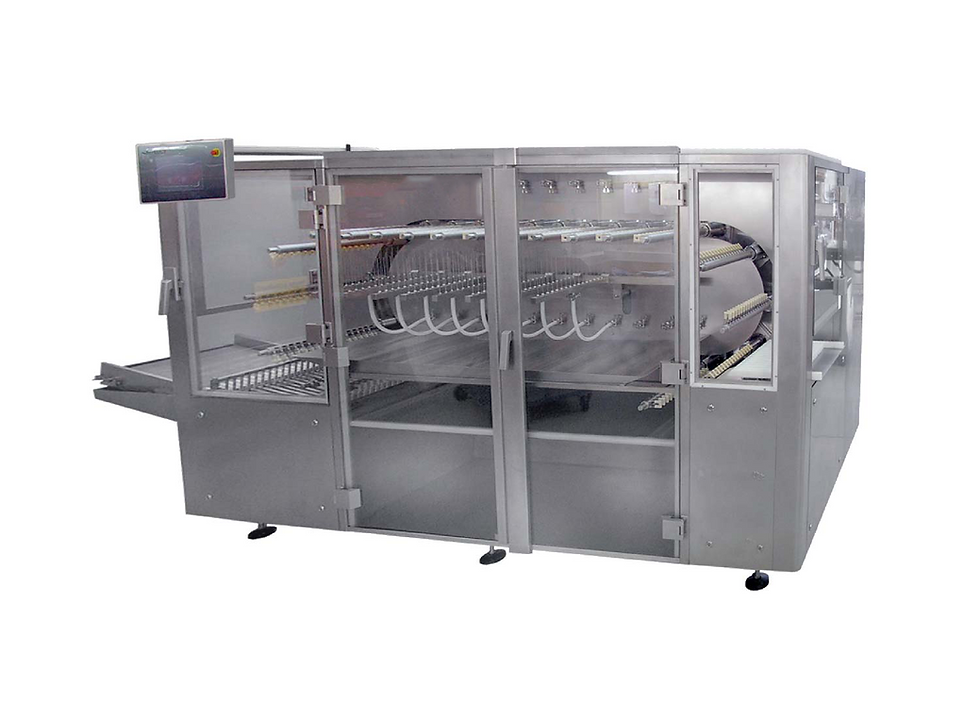
Type 308
Key Features
- Outputs up to 36,000 containers per
hour
- Containers are fed automatically
from an upstream machine or
manually from trays
- Ultrasonic bath for pre-cleaning of
the objects
- No glass-to-glass contact using
coated container grippers
- Specialized cleaning needles
designed to improve energy
efficiency
- Servo motors positioned along the
line guarantee the alignment of the
containers with the washing and
drying needles
The Type 308 is a high-speed machine designed to wash ampoules, cartridges, syringes, and vials. Featuring an innovative balcony design, it allows operators to maintain visual contact with the process. Fully customizable, it offers modules for inside and outside cleaning, inner and outer blow drying, siliconizing, tip cap or needle shield application, and the use of various cleaning agents.

Type 309
Key Features
- Outputs up to 21,000 containers per
hour
- Flexible and compact design allows
for customized cleaning cycles
- Easy access to the cleaning stations
and for size changes
- Quick and easy size changeovers to
process container sizes up to 95 mm
in diameter and 180 mm in height
- Specialized cleaning needles
designed for ideal results and
improved energy efficiency
- Sterile hot air blow drying
parameters are adjustable via the
operator interface terminal
- Optional recycling station, Type 705,
provides cost efficient
reconditioning of used cleaning
agents
The Type 309 machine is a fully automatic, continuous washing system designed for the external cleaning of ampoules, vials, and bottles. It washes, rinses, and dries the external surfaces of the containers, which are then discharged into trays or sent to downstream processing.

Type 401-40X
Key Features
- Outputs up to 610 kg per hour
- Air convection pre-heating and
sterilizing zone for energy efficiency
and gentle heating of the containers
- Containers are fed automatically
from an upstream machine or
manually using trays
- Temperature and differential
pressure indicators ensure ideal and
repeatable machine settings
- Temperature distribution is achieved
by multiple control sensors
- PLC for system control and
monitoring of relevant data
- Servo-controlled baffles aid in cross
flow regulation
The Type 400 series machines offer hot air sterilization for glass ampoules, vials, syringes, and cartridges. The depyrogenation process is divided into three main zones: 1) Pre-Heating, 2) Depyrogenation, and 3) Cooling. These machines can be seamlessly integrated into downstream processing.

Type 302
Key Features
- Outputs up to 24,000 containers per
hour
- Smooth container handling with
coated grippers
- Infeed options from trays or an
upstream machine
- Available ultrasonic bath and
recycling station
- Optional water heating up to 85°C /
185°F
The Type 302 is a rotary washing system designed for cleaning ampoules, bottles, cartridges, vials, and various other containers.

Type 411
Key Features
- Machine designed as a pass-through
into a cleanroom or isolator
- Components are placed into the
chamber by an operator or robotic
arm, and the door is closed to
contain the process
- Complete cycle (loading, exposure,
and unloading) decontaminates the
entire interior of the unit and
container surfaces within 20-60
seconds
- Components are removed and ready
for the next processing stage
- 100% verification on every cycle
- Available as a stand-alone or in-line
machine
The Type 411, Puv-A-Tech™, is an enclosed sterile transfer chamber utilizing pulsed ultraviolet radiation light to decontaminate outer surfaces. This technology achieves up to a 6-log reduction within 5-30 seconds of exposure time.

Type 502/503
Key Features
- Outputs up to 6,000 containers per
hour
- A transport star wheel provides
smooth and continuous transfer of
the objects to the working stations
- Two-piece, valveless dosing pumps
provide precise dosing with filling
accuracy up to +/- 0.05%
- The containers are continually
rotated to minimize foaming of the
product and ensure an evenly
heated ampoule stem, leaving a
perfect dome
- Vials are closed with rubber
stoppers, fed from a vibrating bowl
- Optimized for use under laminar
flow, RABS, or isolator
- The machines can be used as stand
alone units or integrated into a
production line
The Type 502/503 machines combine the filling and closing of ampoules into one single compact unit.
Series 400
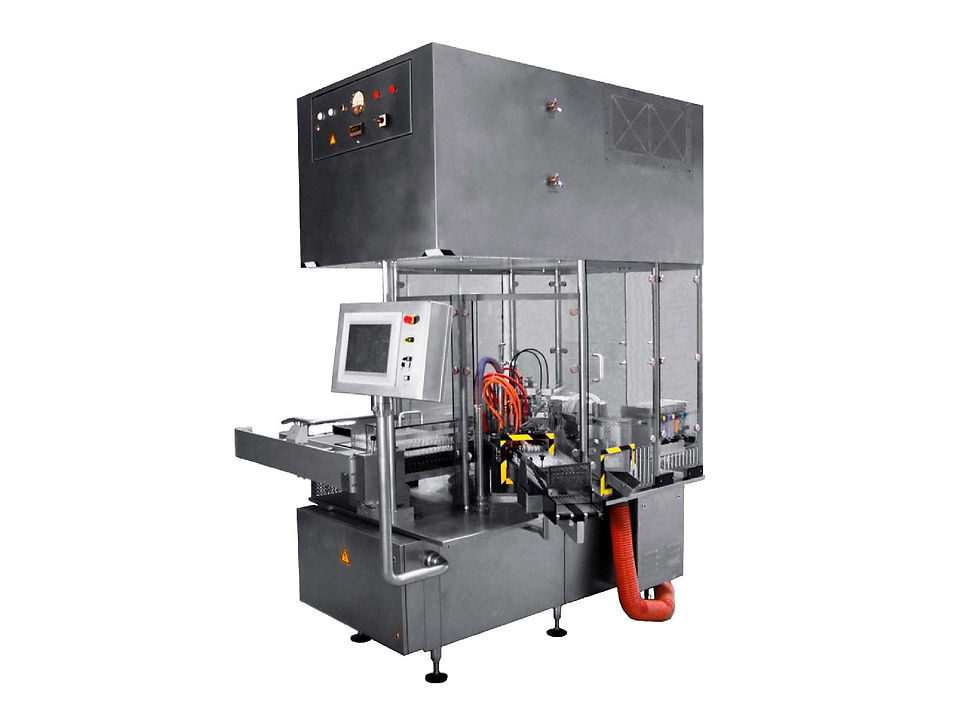
Type 504-506
Key Features
- Outputs up to 24,000 containers per
hour
- Rotary-style machine provides
smooth and gentle continuous
transport of the objects
- System control via PLC
- User-friendly touch screen
operation
- Rotation of the object minimizes
foaming of the product and ensures
an evenly heated ampoule stem,
leaving a perfect dome
The Type 504/505/506 machines are designed for filling and closing both open and pre-sealed ampoules. Their design enables quick and easy changeover from ampoules to vials.

Type 515
Key Features
- Outputs up to 3,600 containers per
hour
- Liquid filling
- Highly flexible and compact design
- Containers are transported into a
star wheel that moves them to
different processing stations
- Filling needles are controlled by a
servo drive for fast and accurate
dosing
- Ultra-high filling accuracy
- Stoppering is fed through a sorting
bowl, picked up by a vacuum tool,
and precisely inserted
- Few size parts, quick changeover
from vials to syringes
- Integrated inspection system
- Laminar flow and/or isolator friendly
design
- Can be used as a stand-alone
machine or integrated into a
complete processing line
The Type 515 is a filling and closing machine designed for vials and syringes. Optimized for use under laminar flow and constructed from high-grade stainless steel, this machine ensures optimum hygienic performance.

Type 515 Plunger
Rod Assembly
Key Features
- Outputs up to 2,400 syringes per
hour
- Compact machine design with
integrated control cabinet
- High precision plunger rod insertion
- Monitored torque for ideal closing
results
- Camera inspection checks for
proper plunger rod and backstop
placement
- Optional labeling station available
The Type 515 combines high-speed plunger rod insertion and labeling of syringes in a single unit. At the heart of the machine is an automated transport star wheel that moves products through four different stations, enabling the assembly of up to 40 syringes per minute. At the first station, a pneumatically actuated gripper assembly picks up a plunger rod from the end of the vibratory track and uses a 2-axis robotic arm to thread it into a syringe. At the second station, backstops are carefully placed on the flange of each syringe. The third and fourth stations check for the presence of the plunger rod and backstop.

Type 529
Key Features
- Available in tabletop, dual, semi
automated conveyor, and fully
automatic versions
- Ideal for lab trials (1 filling head) and
production (2-4 filling heads)
- Peristaltic or mass flow filling
method options
- Attached flow regulator for high
filling accuracy
- Automatically cuts pre-sealed tubes
for filling
- Stoppering and heat/RF/ultrasonic
sealing
- Manual or conveyor belt transport
system
- Integrated closing system
eliminates product contamination
- Compatible with Laminar Flow and
light curtain systems
The Type 529 semi-automatic filling and closing machine for flexible bags sets new standards in the pharmaceutical market. It is capable of processing all bag types (EVA, PVC, PP) with fill volumes ranging from 50 mL to 5 L.

Type 534
Key Features
- Outputs up to 9,000 containers per
hour
- Good accessibility to all
workstations with inline design
- Adjustable walking beam transport
for different container sizes
- Servo-controlled filling needles for
precise filling tolerance up to
+/-0.05%
- Up to 100% in-process control
verification
- Sorting bowls for closures such as
stoppers and caps
- Vacuum-activated placement of
stoppers into vials
- Torque-monitored crimp capping
- Separate container reject and
discharge lanes
- Compatible with RABS, Laminar
Flow, and/or isolator systems
The Type 534 is an automated filling and closing machine designed for vials, bottles, and other free-standing containers. Its modular design allows for easy customization to meet specific customer requirements.
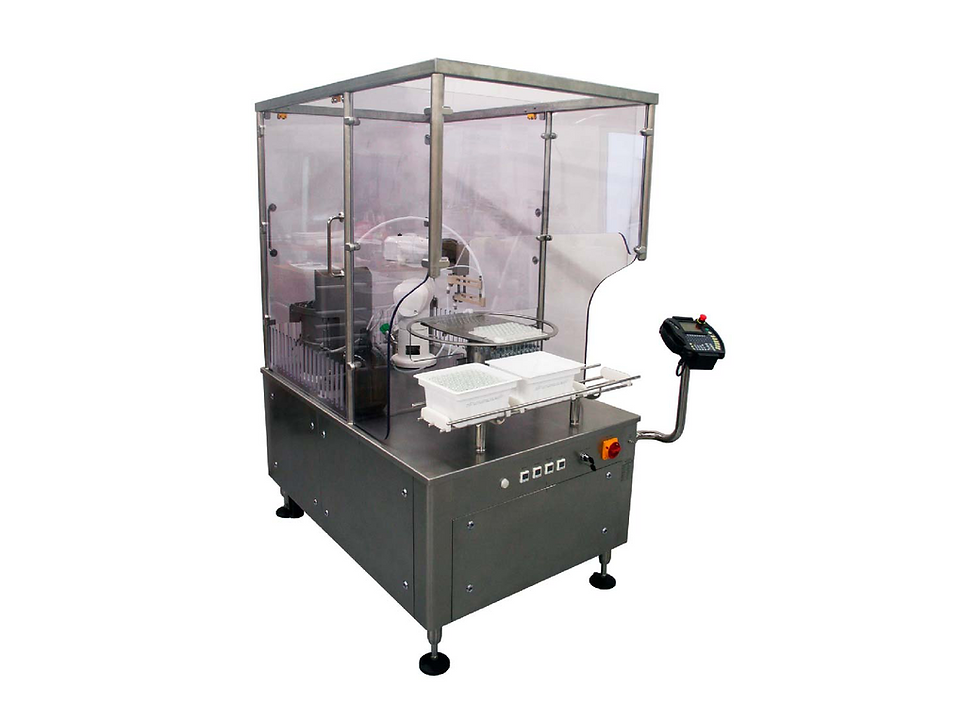
Type 535
Key Features
- Outputs up to 4,600 containers per
hour
- Manual nest loading and unloading
- Turn table in-feed and out-feed
- Rotary piston pump, peristaltic
pump, or time pressure filling
options
- 6-Axis clean room robot or X-Y
transport system
- Sorting bowls for closures
- Filling and closing under vacuum to
reduce contamination and bubble
formation
- Compact machine design with
integrated Laminar Flow
- Machine guarding for optimum user
safety
The Type 535 machine is designed to fill and close nested vials, syringes, and other nested containers. It is the ideal solution for manufacturers seeking to automate and/or validate the filling of products in clinical trials or during the development phase.
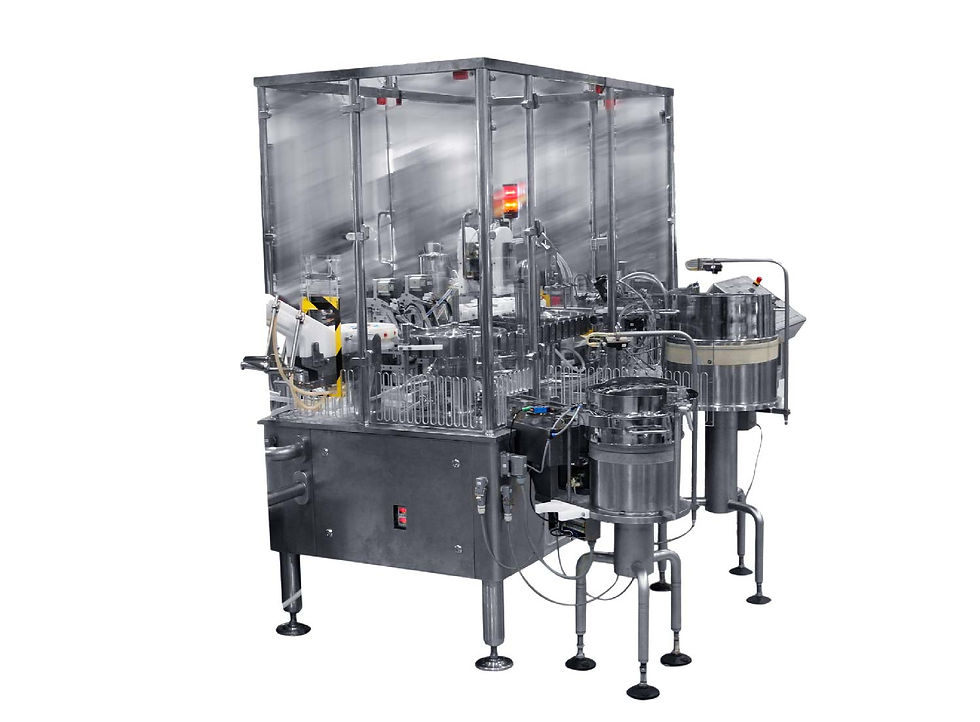
Type 543
Key Features
- Outputs up to 10,000 containers per
hour
- Rotary piston pump, peristaltic
pump, or time-pressure dosing
options
- Customized stoppering station with
vacuum assist
- Direct in-line verification with
camera system
- All parts in contact with the product
can be easily disassembled and
sterilized
- Quick and easy size changeovers
- Containers are transported
separately in individual holders,
which can be quickly changed for
different size containers
The Type 543 filling and closing machine is designed to process vials, syringes, and cartridges with either intermittent or continuous motion throughout the machine. Its modular design allows for easy adaptation to customer-specific requirements.

Type 550
Key Features
- Outputs up to 36,000 containers per
hour
- Processes standard and freeze
dried rubber stoppers
- Best suited for through-the-wall
installations
- Adjustable main transport system
for quick and easy size changeovers
- Containers are separated and
individually fed to the main
transport system
- Optional pre- and post-gassing
available
- Integrated inspection system to
reject faulty containers
- Precision force control for crimping
and integrated visual inspection
system ensures proper sealing
- Balcony design provides optimized
laminar flow friendly operation
inside a Class A clean room and can
be directly combined with an
isolator or a rapid access barrier
system (RABS)
The Type 550 machine features a high-speed, continuous motion balcony design for the filling and closing of vials and cartridges. Its servo drive technology ensures maximum versatility and repeatability.

Type 570
Key Features
- Flexible pick & place modular
platform
- Automatic robot technology for all
processing
- Compatible with isolator and/or
laminar flow systems
- Compatible with lyophilization
transfer chambers
- Robot fills and stoppers nested
containers
- Filling by peristaltic pump with
disposable fill kits
- Custom nest holder for easy
transfer of nested containers in and
out of the processing system
- Robot picks up a bag, inserts the
open tube into the filling needle, and
then seals the tube
The Type 570, Vers-A-Tech™ is a semi- or fully-automatic machine designed to accelerate the packaging of Cell & Gene Therapy products, handling both bags and nested containers on a single platform.

Type 601/602
Key Features
- Outputs up to 24,000 containers per
hour
- Containers are automatically fed
from an upstream machine or
manually using trays
- Individual transport of containers to
the labeling station by a star wheel
- Transport wheel designed with
pockets for safe and gentle handling
of containers
- Precision servo control label
dispenser for self adhesive labels
- Label dispenser is adjustable for
different sizes
- Label dispenser is controlled by a
stepping motor and can be
equipped with additional devices
such as a bar code scanner, printer,
or checking units
- User-friendly touch screen
operation
- Easily exchangeable size parts allow
for various container sizes
- Containers are discharged into trays
- Station can be equipped with a hot
foil, thermal transfer, laser, or ink jet
printer
- Horizontal and vertical adjustments
of the printer adapt to different print
areas
- Rubber roller dispensing station
ensures smooth label application on
containers
The Type 601-602 machines are compact, fully automatic systems designed for printing and applying self-adhesive labels to vials, bottles, syringes, ampoules, and cartridges. These continuous motion labelers can be integrated into a production line or operated as stand-alone machines.
Series 600

Type 603
Key Features
- Outputs up to 36,000 containers per
hour
- Quick, tool-free size part changes
- Easy accessibility to all working
stations
- Smooth, continuous container
transport
- Automatic rejection of
nonconforming objects
- Safety system ensures user
protection
- User-friendly touch screen
operation
- Integrated electronic control cabinet
in the machine base
- Can be equipped with a bar code
scanner, vision system, and various
printer types
The Type 603 is a fully automatic labeling machine designed for applying self-adhesive labels to vials, cartridges, ampoules, and other special containers. It can function as a stand-alone labeler or be integrated into a fully automatic production line.

Type 604
Key Features
- Outputs up to 12,000 containers per
hour
- Highly flexible and compact design
- Label dispenser unit with servo
technology
- Automatic speed synchronization
- User-friendly touch screen
operation and system control via
PLC
- Accurate placement of labels on
containers
- Options available for barcode
scanner, label position and presence
check, and printer
The Type 604 is a fully automatic, linear machine designed to apply self-adhesive labels to bottles. Labels are printed by a hot foil, thermal transfer, or laser printer and then transferred to the labeling station. Containers are fed from an upstream machine by a rotary table or conveyor to complete the label application process.

Type 607
Key Features
- Outputs up to 24,000 syringes per
hour
- Servo-controlled main drive and
rotation motion of the syringe
produce precise and constantly
monitored torque
- Rotary movement of syringes to
ensure smooth positioning
- Torque feedback allowing for
automatic adjustment of insertion
- Integration of hot foil, inkjet, or laser
printers
- Vision system for validating correct
label information
- Automatic rejection of non
conforming containers
- Can be used as a stand-alone
machine or integrate into a
processing line
The Type 607 is a compact machine that combines high-speed plunger rod insertion, backstop assembly, and labeling of syringes. It can process various types and sizes of syringes, plunger rods, and backstops with the use of interchangeable size parts.

Type 703
Key Features
- Outputs up to 36,000 objects per
hour
- Adjustable infeed guides to process
various container sizes
- Transport of containers to the
loading station via servo driven
transport belt
- Configurable for various types of
trays (e.g., stainless steel,
cardboard, 3-sided trays)
- Camera verification system
- Automatic rejection of non
conforming objects
The Type 703 tray loader is a precise and compact solution for loading containers into trays. It can handle various sizes of vials, bottles, syringes, ampoules, cartridges, and other stable standing containers. A fully integrated camera system ensures all quality standards are met.
Series 500
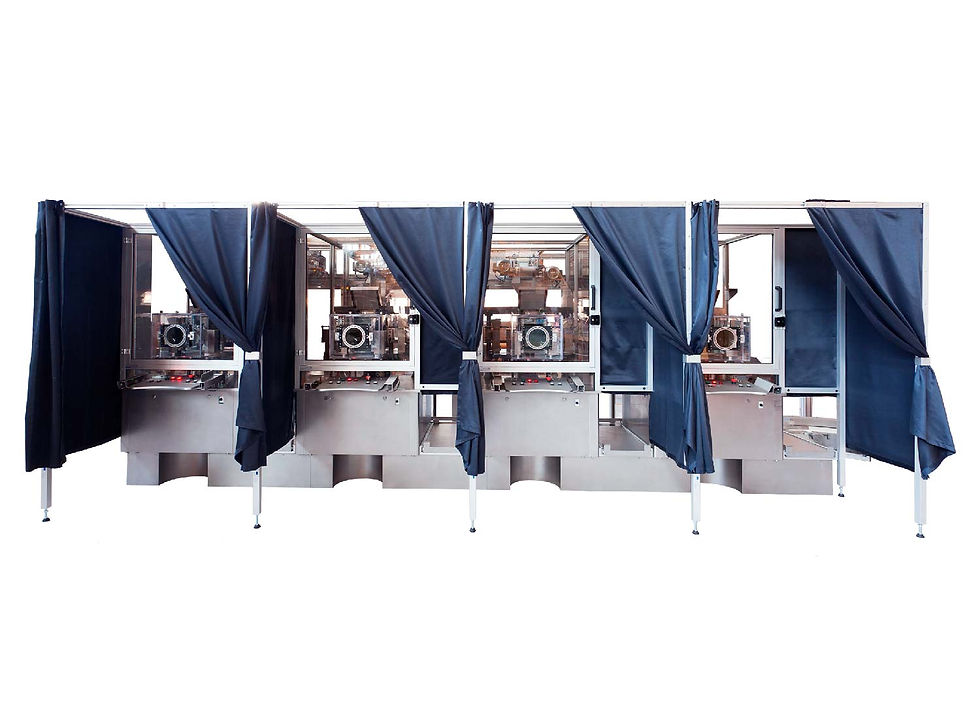
Type 728
Key Features
- Non-conforming bags are rejected
from the machine
- Upgradable features include
conveyor belt infeed, report data
printing, dark protection curtains,
and spare/wear parts