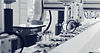
Solutions
Operations
Labelling
Overview
Our Type 600 series labeling machines are compact solutions for printing and applying self-adhesive labels to various containers, including vials, syringes, bottles, cartridges, and ampoules. These continuous motion labelers can be integrated into a production line or operated as stand-alone machines.
Benefits
- Great flexibility in labeling various container types and
sizes
- Size parts can be quickly and easily changed without
tools
- Print station can be equipped with a hot-foil, thermal
transfer, or laser printer
- Labels are accurately placed on each container
- Servo-driven for high precision
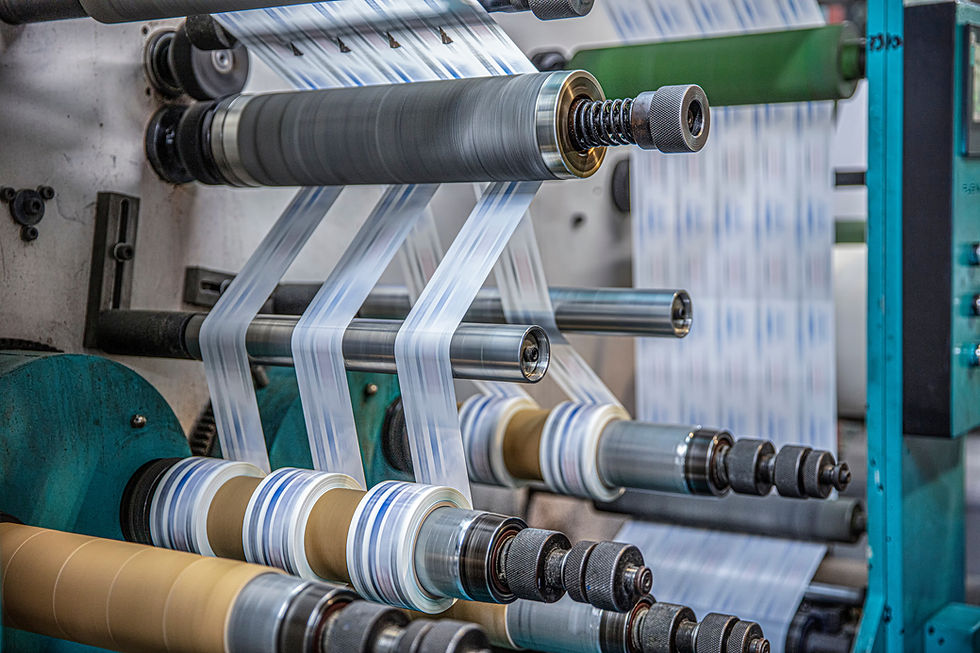
Loading & Sealing
Overview
Our Type 500 series machines specialize in loading and sealing liquids into a wide variety of containers and container sizes. These machines are custom designed to meet your specific container types and output ranges, whether low, medium, or high. The loading and sealing machines can be integrated into upstream and downstream fill-finish processes and are compatible with laminar flow units and isolators for optimal environmental control.
Benefits
- Filling accuracy achieved by rotary piston, peristaltic, or
time pressure pump
- Servo-controlled filling needles for precise tolerances
up to +/- 0.05%
- Up to 100% In Process Control verification
- Sorting bowls for container closures
- Vacuum-activated placement of stoppers into
containers
- Torque-monitored capping
- User-friendly touchscreen operation and system
control via HMI
- Laminar airflow operation inside a Class A clean room,
compatible with isolator or RABS (rapid access barrier
system)
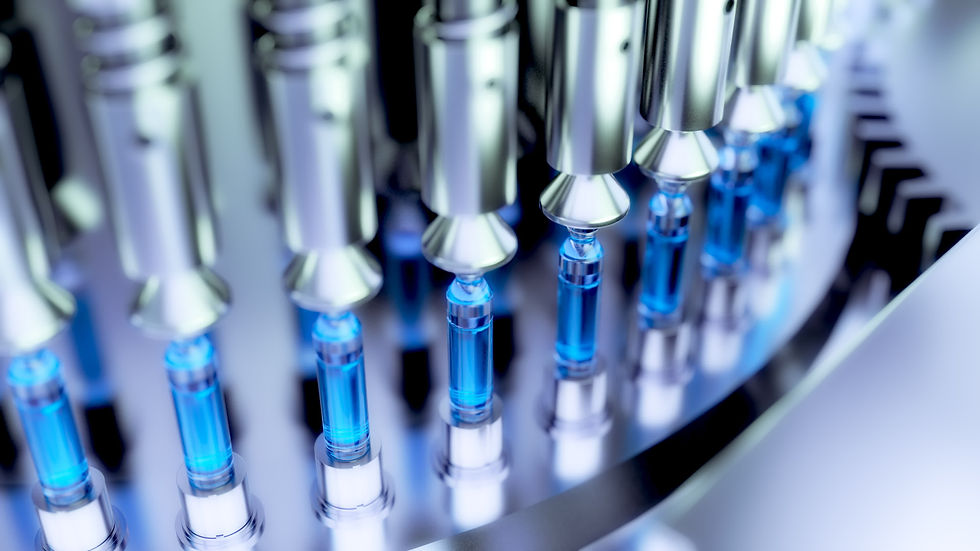
Sterilizing
Overview
Our Type 400 series machines are designed for dry heat depyrogenation, sterilization, drying, and silicone coating of individual glass containers. The process utilizes recirculated hot air across three zones: (1) pre-heating, (2) depyrogenation, and (3) cooling. This method effectively removes pyrogens, with endotoxin destruction as the primary goal. The extremely high temperature (330°C) destroys all contaminants down to carbons, providing absolute sterilization. The Type 400 series machines can be integrated with upstream washers and downstream fill-finish processing.
Benefits
- Class A (100) cleanroom specifications met with heat
resistant, high-capacity particle filters
- Air convection pre-heating and sterilizing zone for
energy efficiency and gentle heating of the containers
- Wire mesh transport system allows for optimal hot air
laminar airflow
- Sterilization of vials, syringes, cartridges, bottles, and
ampoules
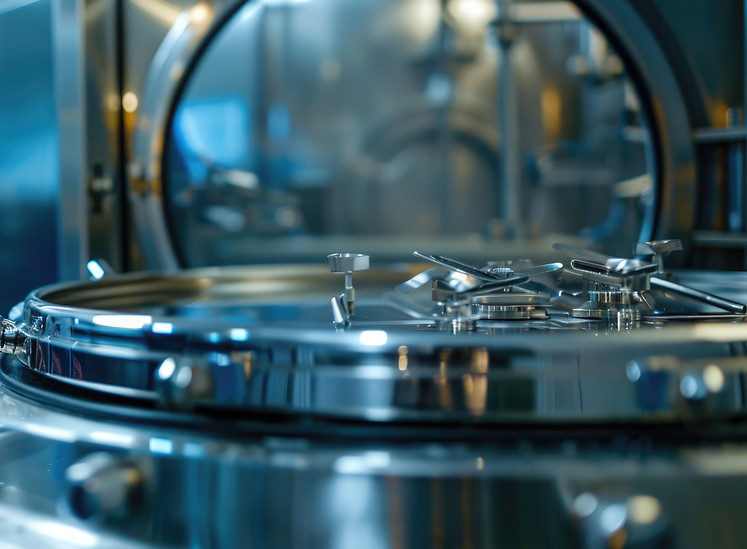
Washing
Overview
Our Type 300 series machines wash and dry the inside and outside of bulk vials, syringes, bottles, cartridges, and ampoules. Coated grippers gently move the containers between stations, utilizing various cleaning agents. These modular machines can function as stand-alone washers or be integrated into a fully automated line.
Key Features
- Smooth object handling by coated grippers
- Quick and easy size changeovers
- Cost-effective WFI recycling unit
- Internal cleaning and drying at up to 11 stations,
including ultrasonic pre-washing
- Several different cleaning agents can be used
- Energy-efficient cleaning needle design
- Cleaning process can be extended with additional
modules such as siliconization or needle shield
insertion station
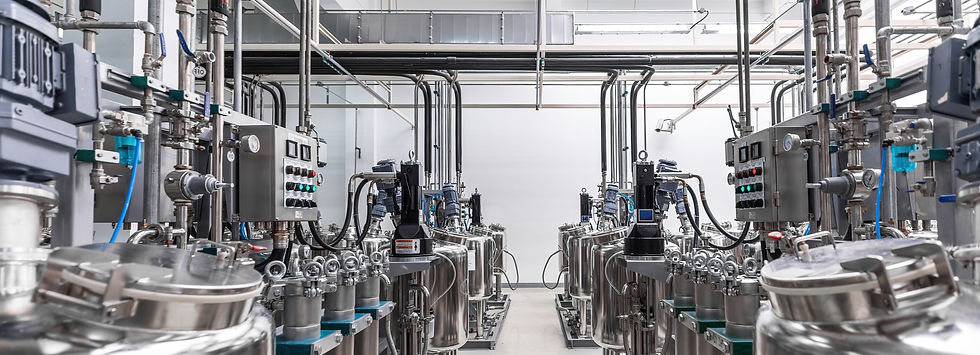
Machines by Operation
Labelling
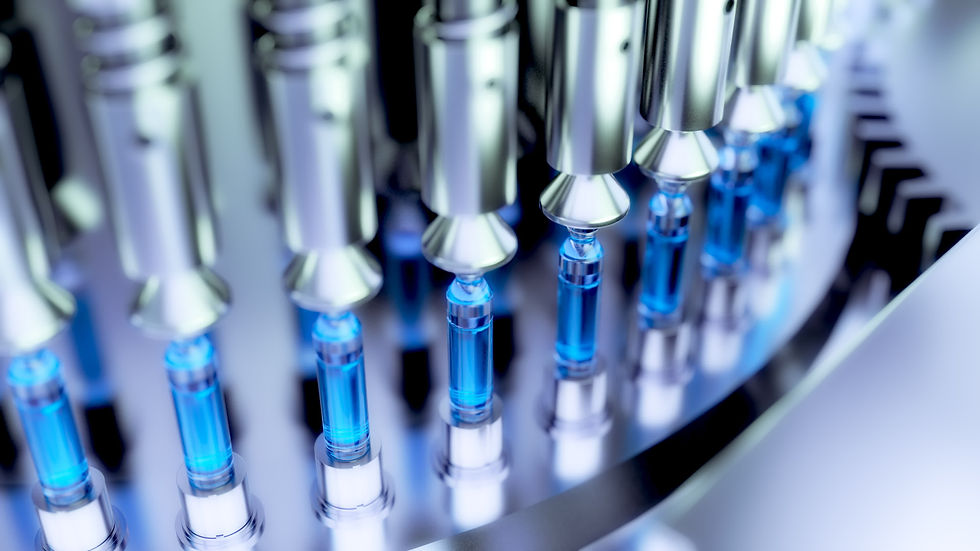
Overview
Benefits
- Filling accuracy achieved by rotary
piston, peristaltic, or time pressure
pump
- Servo-controlled filling needles for
precise tolerances up to +/- 0.05%
- Up to 100% In Process Control
verification
- Sorting bowls for container closures
- Vacuum-activated placement of
stoppers into containers
- Torque-monitored capping
- User-friendly touchscreen operation
and system control via HMI
- Laminar airflow operation inside a
Class A clean room, compatible with
isolator or RABS (rapid access
barrier system)
Our Type 500 series machines specialize in loading and sealing liquids into a wide variety of containers and container sizes. These machines are custom designed to meet your specific container types and output ranges, whether low, medium, or high. The loading and sealing machines can be integrated into upstream and downstream fill-finish processes and are compatible with laminar flow units and isolators for optimal environmental control.
Sterilizing
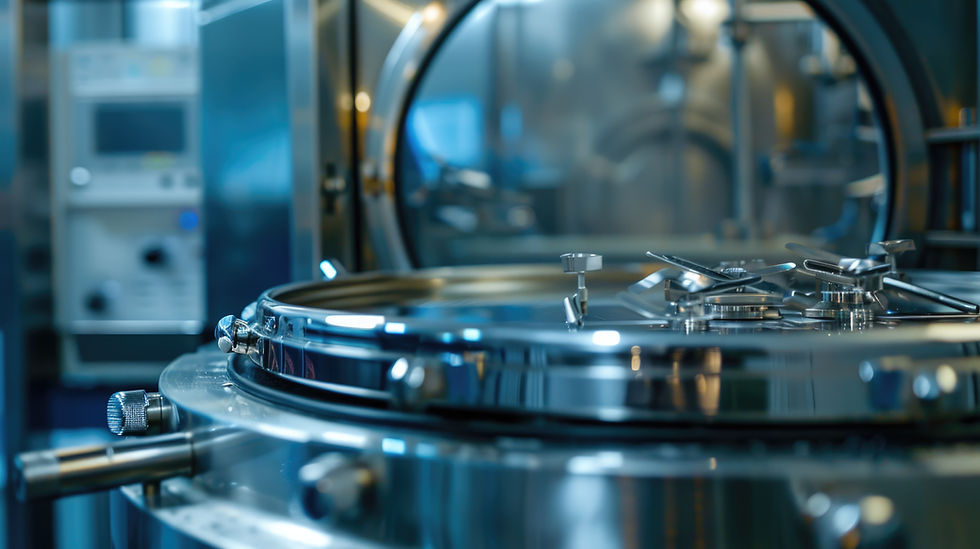
Overview
Benefits
- Class A (100) cleanroom
specifications met with heat
resistant, high-capacity particle
filters
- Air convection pre-heating and
sterilizing zone for energy efficiency
and gentle heating of the containers
- Wire mesh transport system allows
for optimal hot air laminar airflow
- Sterilization of vials, syringes,
cartridges, bottles, and ampoules
Our Type 400 series machines are designed for dry heat depyrogenation, sterilization, drying, and silicone coating of individual glass containers. The process utilizes recirculated hot air across three zones: (1) pre-heating, (2) depyrogenation, and (3) cooling. This method effectively removes pyrogens, with endotoxin destruction as the primary goal. The extremely high temperature (330°C) destroys all contaminants down to carbons, providing absolute sterilization. The Type 400 series machines can be integrated with upstream washers and downstream fill-finish processing.
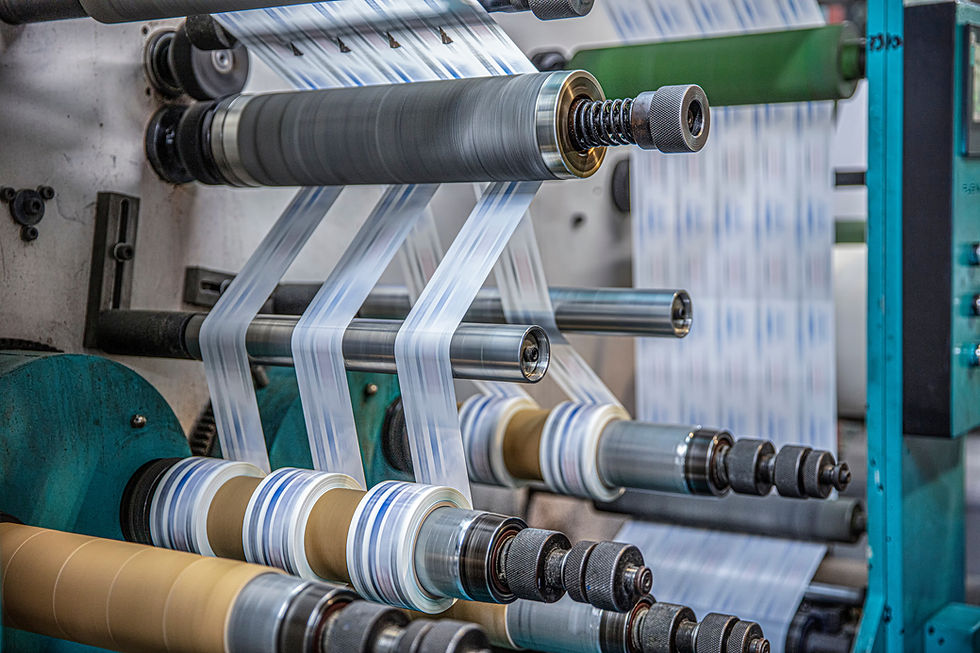
Overview
Benefits
- Great flexibility in labeling various
container types and sizes
- Size parts can be quickly and easily
changed without tools
- Print station can be equipped with a
hot-foil, thermal transfer, or laser
printer
- Labels are accurately placed on each
container
- Servo-driven for high precision
Our Type 600 series labeling machines are compact solutions for printing and applying self-adhesive labels to various containers, including vials, syringes, bottles, cartridges, and ampoules. These continuous motion labelers can be integrated into a production line or operated as stand-alone machines.
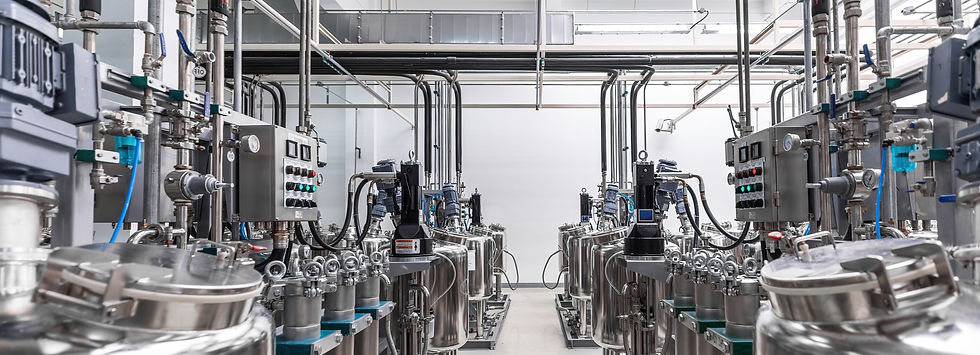
Overview
Benefits
- Smooth object handling by coated
grippers
- Quick and easy size changeovers
- Cost-effective WFI recycling unit
- Internal cleaning and drying at up to
11 stations, including ultrasonic pre
washing
- Several different cleaning agents
can be used
- Energy-efficient cleaning needle
design
- Cleaning process can be extended
with additional modules such as
siliconization or needle shield
insertion station